Motor Control Interface
AmePower's Motor Control Interface (MCI) is a high-tech system for trains, using advanced technology to efficiently control the train's motors and improve energy efficiency.
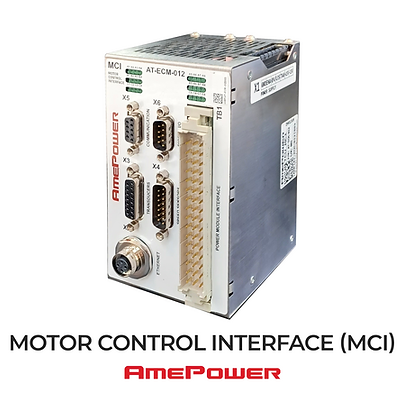
FEATURES:
-
Cutting-Edge Technology: MCI boasts an EN 50155 compliant SmartFusion2 SoC with a 32-bit ARM Cortex M3 processor, enhancing efficiency and safety. Equipment used on rolling stock
-
Precision Propulsion Control: Advanced algorithms enable precise acceleration, deceleration, and speed management for a smooth train ride.
-
Adaptive Intelligence: Constantly monitoring operational conditions, MCI dynamically adjusts power distribution, traction control, and braking mechanisms for optimal energy efficiency and passenger safety.
MAINTENANCE
Learn about AmePower's MCI, understand its safe and low-maintenance design, and ensure proper procedures for spare parts and end-of-life disposal..

SAFETY GUIDELINES
-
Before installing or removing the MCI unit, ensure the power is disconnected from the system.

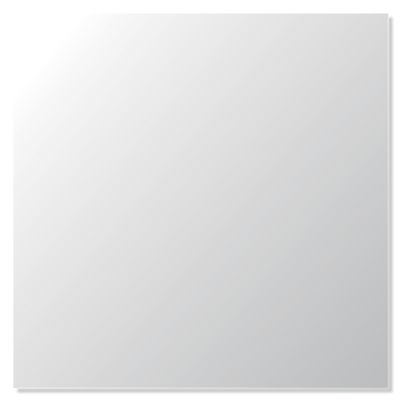
NO MAINTENANCE REQUIRED
-
The MCI requires no maintenance throughout its operational life.


SPARE PARTS PROCEDURE
-
List and drawings of spare parts are not provided. Failed units must be returned to AmePower for analysis and repair.


END-OF-LIFE DISPOSAL
-
At the end of their service life, replace corresponding modules professionally and dispose of old ones following local, regional, and national regulations.

INTEGRATE YOUR TRAIN PROPULSION SYSTEM WITH AMEPOWER'S MOTOR CONTROL INTERFACE
MCI SPECIFICATIONS
The Motor Control Interface, AT-ECM-012 module is a motor controller that features a SmartFusion2, a system-on-chip with a 32-bit ARM Cortex M3 processor core with integrated hard-IP I/O peripherals and a flash-based FPGA fabric Flash FPGA. The MCI module is designed to drive a 3-phase induction motor and a brake chopper by means of vector control. It has been designed according to EN50155:2017 and IEC 60571:2012 standards for railway applications.
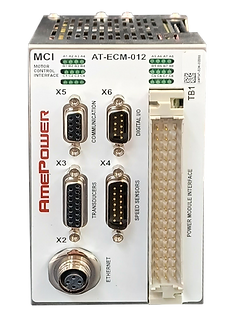
FEATURES
-
EN 50155 compliant
-
Wide input supply voltage range
-
CAN and RS-485 communication
-
Measurement of 2 rotary encoders with A 90° B signals
-
Up to 8 analog current input channels + input voltage monitoring

The MCI features 24 LEDs that depict its operating status.
Dimensions
Connectors
Environmental Specifications
MCI TECHNICAL DATA
Electromagnetic Compatibility
The MCI module complies with the EN 50121-3-2 standard (electromagnetic compatibility for equipment used in railroad applications). To ensure trouble-free operation of the devices, an EMC-compliant electrical installation is necessary. The system integrator is responsible for ensuring that the device is not exposed to sources of interference that cause disturbances at levels higher than those defined in EN 50121-3-2.